An In-Depth Look at Methods Protomatic Uses to Inspect Parts
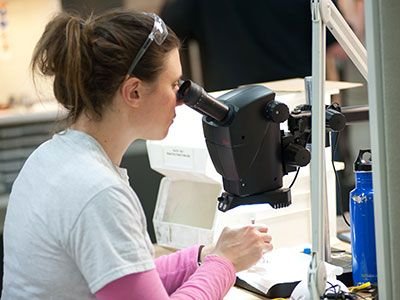
Inspecting parts is a crucial stage in the manufacturing process. In order to maintain a quality level of Life-Saving Precision, Protomatic takes specific steps to ensure that the parts produced meet rigorous standards.
Why does the Quality Department sample?
The sampling method of analysis has shown that the process of selecting a random sample and measuring characteristics from a population of interest provides an accurate representation of the whole population.
An example of a real-life application would be to conduct a poll to predict the winner of an upcoming election. In the manufacturing world, an example is inspection of a sample of parts to determine if the entire lot meets requirements.
Sampling is a good approach, but you need to be aware of its limitations. Most sampling systems rely on having a random sample. If the sample is skewed at all, the results will be inaccurate. So, if you don’t have a completely random sample, applying the results to the entire population would lead to inaccurate conclusions.
What can go wrong with a biased sample?
Historically, statistical prediction errors have occurred. One of the most infamous examples was the 1936 presidential race between FDR and Alf Landon, an important presidential race at the height of the Great Depression.
Earlier, in 1932, Literary Digest had conducted a “Straw Poll” and accurately predicted the outcome. They repeated the poll in 1936. This time the sampling size was very large — 10 million households were sent surveys, with a 2.4 million response rate. That was quite a significant response with a total US population of about 140 million at that time.
Although the sample size was very large, the sample was not random. The survey was conducted with voluntary Digest readers, automobile owners, and telephone users. This sample did not represent the US population because all had disposable incomes well above the national average. The result was flawed, with the incorrect prediction of Landon winning.
In comparison, George Gallup’s American Institute of Public Opinion correctly predicted the results of FDR winning the election using a sample of only 50,000.
The analysis demonstrated that a large sample from a skewed population does not predict the correct results. So guidelines have been established with various sampling methods.
Military origins
Some of the most common sampling methods come from the military. Many of these have been made obsolete by improved standards, but are still in use. The most popular, MIL-STD-105, was a United States defense standard that provided procedures and tables for sampling by attributes based on sampling inspection theories and mathematical formulas.
However, today the Department of Defense preferred method of product acceptance is MIL-STD-1916. The goal of this new standard is to support the movement away from an AQL-based detection strategy to implementation of a prevention strategy. It includes a comprehensive quality system, continuous improvement and a partnership with the government.
The MIL-STD-414 application has also been vastly improved. You can now design plans for both known and unknown variability, and the application has been completed to include all three types of inspections. This application designs a sampling plan for variables, according to the Military Standard 414 tables, for a given lot size and AQL. It also calculates the estimated percent defectives in a lot, given the known or estimated variability.
Lot-by-lot inspection
C=0 (Zero Acceptance Number Sampling Plans), are a set of attribute plans for lot-by-lot inspection with the acceptance number in all cases as zero failures. After years of extensive application by government contractors, commercial manufacturing, and service industries, these C=0 sampling plans are now considered standalone sampling plans and are today’s norm.
The zero acceptance number plans were originally designed and used to provide equal or greater consumer protection with less overall inspection than the corresponding MIL-STD-105-E sampling plans.
Boeing standards
A seller to Boeing must perform 100% inspection for in-process and final inspection or shall conform to requirements of document D1-8007 “Approval Guide for Supplier Statistical Plans.” A seller that performs statistical methods for product acceptance at receiving, in-process or final inspection must have Boeing-approved procedures and/or plans, as required by D1-8007, prior to implementation of statistical methods.
For more on quality and inspection methods, please visit the American Society for Quality website.
Specific methods for specific needs
At Protomatic, we use all these methods and additional customer specific methods. Each industry we work with has a different need. Some customers always order in small batch sizes. These parts are typically 100% inspected and sampling does not apply. For customers that run medium (100+) to large batch sizes (100,000+), sampling programs are very beneficial in reducing part cost.
Another consideration is the complexity of the parts. Some parts have a small number of tools used to manufacture, some parts are very complex, utilizing 40-60 tools to complete. More tools mean more variation or modes of failure. Almost all of our customers require extremely high part quality, so we adjust from 100% inspection to a sampling plan based on need.
Economics of sampling
Next month we will talk about the economics of sampling – a simple way to understand the cost of inspection.
Inspection methods are just one of the many considerations when choosing a CNC machine shop. For a complete list of things to look for, please download the free guide, Tips for Choosing a Prototyping Machine Shop.
Many of the thoughts in this article came from a document titled “Advantages and Disadvantages of Sampling,” by Jeffrey S. Solomon.
About the author: Doug Wetzel is Vice President and General Manager of Protomatic. Protomatic is a CNC precision machining shop specializing in prototype and short-run production components for the medical, aerospace and other technical industries. Because of the critical nature of the parts they design and manufacture, the emphasis is always on Life-Saving Precision.