Are you getting the right CNC machine for your job?
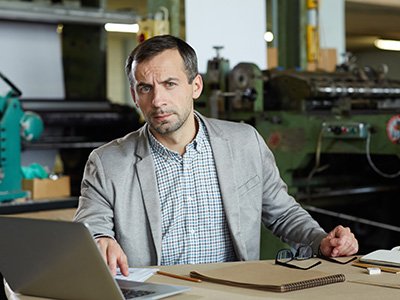
It is critical that the the CNC equipment selected for your job will produce optimum results. Guesswork won’t work.
At Protomatic, the process begins in our detailed Production Planning Procedure. This involves a multi-discipline team of Engineering, Purchasing, Quality and Manufacturing representatives.
The first phase of the process identifies the conditions for the job through a Production Planning Checklist. This comprehensive checklist provides information on the job to help identify the needs as related to each interrelated department.
Engineering Department
For example, the Engineering Department provides details including, but not limited, to:
- Making prints and specifications available on Engineering Share
- Converting Solidworks to IGES or usable math data
- Preparing material/supplier sheets
- Verifying print deviations
Quality Department
The Quality Department offers information of subjects such as:
- Confirmation that ordered material meets requirements
- Repeat part history
- In-Process Inspection Worksheet
- Final inspection worksheet
- Inspection gages
Manufacturing Department
The checklist from the Manufacturing Department includes:
- Verifying material is ordered
- Specifying special tools
- Confirming technicians are properly trained
Upon completion of the checklist, the manufacturing manager will have a thorough understanding of the job needs that go over and above the Blueprint or CAD Data. With this information, the manufacturing manager schedules, then selects the CNC equipment based on
- Equipment Size
- Performance Specification of Machine (Spindle horsepower, maximum RPM, and feed rate)
- Equipment availability
- Machine accuracy
The next phase is more difficult
The next phase turns the difficulty dial up a few notches. The Manufacturing Manager now selects the personnel appropriate for the designated difficulty level of part. From the most simple to incredibly complex parts, each and every part we manufacture requires specialized technical training.
At Protomatic, since many of our jobs are being manufactured for the first time, programming is required. Machine tools such as endmills, drills, etc. are setup; their electronic offsets are set (Inputted) in the CNC controller; part-holding fixtures are setup; then finally, the program trial part is run.
It is time to inspect and adjust
Once the trial part is manufactured, we confirm that it meets the part’s meets dimensional requirements. This typically requires quality inspection to confirm GD&T requirements. If adjustments are required, the machine’s programming must be modified accordingly. If a job is a repeat order, operators, a machinist or senior machinist may be required to re-setup the part. This is an extremely important phase of manufacturing, and due to its complexity is a focus of ongoing training.
No room for error
Because the parts we manufacture for the medical, aerospace and other technical industries are of such a critical nature, there is simply no room for error. By being uncompromising in detail from the initial process checklist to final manufacture and inspection, our commitment is always to Life-saving Precision.
CONTACT US DIRECTLY. Phone 734-426-3655
- Scott Allen, Sales Manager Scott@Protomatic.com
- Lori Franz, Sales Lori@Protomatic.com
- Doug Wetzel, VP/GM Doug@protomatic.com
- Brian Heldt, Program Manager Bheldt@protomatic.com
About the author: Doug Wetzel is Vice President and General Manager of Protomatic.