Broken Tool Detector
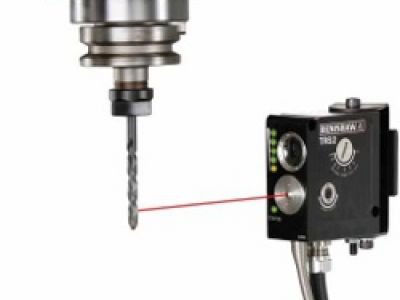
This month Protomatic is highlighting a small, but very powerful equipment addition to our new Vertical Milling Center. This option is being integrated to the Haas VF-2SSYT that was added last month.
Renishaw TRS2 Non-Contact Broken Tool Detector
Shown here is a simulation of the laser beam measuring the length and diameter of the drill. This is performed 200, 1000 or 5000 RPM.
The Tool Detector works on all types of spinning tools including drills, endmills, taps, and reamers
Automation Improvements
Protomatic is actively improving product reliability. For example, failed tapping operation due to a broken drill is a significant event affecting part quality. A Tool Detector system is just one of the accessories that can be used to verify that a machining operation has been successful and the next operation can proceed.
How the Tool Detector works
The TRS2 is a laser-based, non-contact system that provides high-speed and very accurate detection of a broken tool. As a tool is moved into the laser beam, the system detects its reflection. Within a second, the output signals of the detector are sent to the controller which verifies the presence of the tool. If a no reflection is received, a broken tool alarm is raised and an equivalent replacement tool is selected from the magazine system. Detection takes place during the rapid feed rate to allow the “halt process” to take place if necessary. This occurs when the tool initially moves in rapid motion to the checking position in the spindle axis utilizing the active tool length offset. The TRS2 system confirms the offset location of the tool to determine if the tool can be relied upon for the entire machining event.
Increasing Product Reliability
This is just one of the ways the Protomatic team is improving your product quality without sacrificing productivity. Although the replacement of a broken tool takes a few seconds for the tool selector magazine to index, this process enhancement increases the reliability of the machining operation