Don’t Sweat the Small Stuff. CNC Machining of Small Parts.
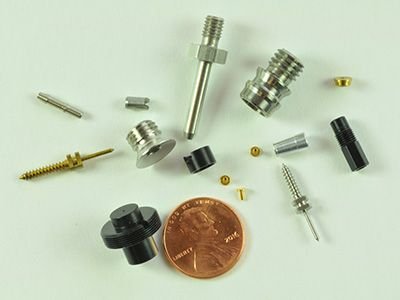
Technically small parts are hard to make. As you get smaller, challenges arise. Deburring, machine accuracy and tool quality are just some of the problems that are experienced when making small part features. Protomatic has the equipment, tools and expertise required to successfully manufacture the tiniest of parts.
Inspection Equipment
Features smaller than 0.005’’ are hard to see with the naked eye. Accurate inspection is one of the major difficulties in manufacturing small parts or large parts that have small features. Manufacturing and inspecting is all about being able to see what you are making. At Protomatic, we have an array of equipment including vision systems, a 3D microscope, and optical and video-based microscopes. This equipment varies from 10x-200x focal power. Additionally, we use special equipment such as light fibers to apply light to the hardest to see areas.
For small features, we can measure with the 3D microscope or a Tallysurf Intra. The Tallysurf can measure features 1mm (0.040”) vertical range with 16nM resolution. This allows measurement of features and accurately measures surface finishes.
All of this equipment is used to inspect parts, but we also inspect tools prior to use. An incorrectly ground drill will break on the first hole, so it is critical to inspect micro tooling prior to use.
Special Drilling and Milling Equipment
Not only do you have to have specialized inspection equipment, but the manufacturing equipment is important. High RPM equipment is one of the most important tools for success. Protomatic has various high speed spindles capable in the 0-85K RPM range. This allows us to use small drills and cut at their optimum revolutions per minute.
An example of calculating optimum cutting speed is demonstrated in an easy three-step process.
- Look up the material and tool optimum cutting speed in SFM.
- Select diameter of cutting tool.
- Calculate RPM per the following formula: RPM = 3.82 x SFM / diameter
RPM Calculation Example:
Calculate the RPM required for a 0.003’’ diameter drill with above formula
Material and Tool combination is designed to cut at 25 SFM, drill 0.003’’RPM=3.82 x SFM/diameter=3.82 x 25 / 0.003 = 31,833 RPM
A Second Calculation with a smaller drill:
If the hole diameter is reduced to 0.002”, the required RPM calculation is now:
RPM = 3.82 x 25 / 0.002 = 47,750 RPM
In comparison, as the diameter decreased, the RPM for the optimum cut increases significantly.
What are the practical limits?
The practical limit for drilling is about 0.002” (0.050mm) and endmills are available to 0.008” (0.200mm). Although tools are available in smaller sizes, these tools are very fragile, and can easily be damaged. Additionally, the quality of tools is less consistent and a good percentage will be rejected prior to use.
Why is there a push to go smaller?
Theoretical strength of materials
Manufacturing techniques allow for more theoretical performance of the base material. This is due to minimized voids and imperfections. Imperfections disrupt the ionic, metallic-covalent or Van Der Waal bonds, which will lead to weaker materials and parts. Smaller parts may also have other properties for improved performance, such as being small enough that the coefficient of expansion may not be significant. Or the smaller mass may allow for improved performance when heat treating or plating.
Smaller can be better
Clearly there are advantages to making parts smaller. The product can be lighter and may use less energy or be more efficient. But a design for small sizes inherently creates the need for manufacturing and engineering to validate the best product performance goals.
Large Challenge
As parts get smaller, the challenges of successfully designing, manufacturing, and measuring them get larger. It takes a significant investment in training, expertise, tooling and metrology to consistently produce the highest quality small parts.
Protomatic sweats the small stuff so you don’t have to. We have the tools and the experience to manufacture even the most intricate small parts. To learn how we use this expertise in machining with Life-Saving Precision, download our free eBook, “Tips for Choosing a Prototyping Machine Shop.”
About the author: Doug Wetzel is Vice President and General Manager of Protomatic. Protomatic is a CNC precision machining shop specializing in prototype and short-run production components for the medical, aerospace and other technical industries. Because of the critical nature of the parts they design and manufacture, the emphasis is always on Life-Saving Precision.