How to Tell the Difference in CNC Machine Shops
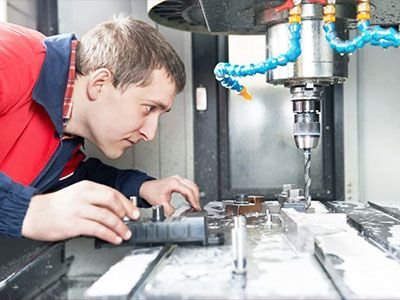
When looking for a CNC machine shop for your next prototyping job, whether it’s manufacturing prototypes for aerospace components or medical devices, there are a few things you should check out before giving a thumbs up. By asking the right questions and digging beneath the surface you’ll be much more likely to find a CNC machine shop that is a great fit for you.
1) Do they have the right equipment?
It is vital that the CNC shop you choose has the machinery to give your prototype the life-saving precision it deserves. This is particularly true in the aerospace and medical industries.
One of the first things to check on is whether they have at least 4- or 5-axis machinery. Some CNC job shops, like Protomatic in Dexter, MI, have as much as 8-axis machines.
Like anything, there are pluses and minuses to having multi-axis capabilities. First, the downside (although its really not all that bad). Unfortunately, multi-axis machines come with a higher hourly rate. When you stop a minute to think about it, it just makes sense.
Because of the multi-axis capabilities, it takes longer to program each machine. It also takes more time to set up, and the machinery itself is inherently more expensive.
BUT…multi-axis machines are much more accurate because they don’t require re-clamping. So, for instance, instead of re-clamping and taking three operations, a multi-axis machine can do it all in one — and since there is no re-clamping, there is minimal chance of losing accuracy.
When you consider that many CNC projects involve machining to one-thirtieth the thickness of a sheet of paper, the importance of accuracy is more evident than ever.
You may also want to know if the shop has a multi-axis machine with an articulating head, which can further ensure accuracy. That may be overkill for what you need. But maybe not. It’s better to find out ahead of time and be safe rather than sorry.
2) Are they experienced in the metals you need?
More and more, every day, industry is using exotic alloy metals. They are particularly being used in high-temperature applications for aerospace components such as rocket engines and rocket valves. These nickel-based alloys such as Inconel®, Hastelloy®, chromium, tungsten, and invar are tough to work with. If you need them, you will definitely want to know that the CNC machine shop you choose has successfully worked with them before. Not many have.
Protomatic is one of the shops that offers that experience. Recently we took a round bar of 625 Inconel®, machined it into a square tube, and held it flat for 3/1000th of an inch over the entire 2 ft. part. That’s just one example of many.
There have been times, though, when we’ve turned a project down because it wasn’t a good fit for our capabilities. In cases such as that, we won’t subcontract it to someone else because of reliability concerns — especially for aerospace components and medical devices.
With that in mind, I recommend that if you’re talking to a shop about machining alloys, you ask if they are going to do it themselves or contract it out. For your particular job, it may or may not be a big deal. But it never hurts to know.
While machines and materials are certainly the two biggest areas to check out when choosing a CNC machine shop, there are obviously others. You may also want to check out accreditations, experience in your industry and the size of part the shop can handle.
The more you know, the better the chance you’ll choose the right shop for your job, and will have a successful result.
About the author: Doug Wetzel is Vice President and General Manager of Protomatic. Protomatic is a CNC precision machining shop specializing in prototype and short-run production components for the medical, aerospace and other technical industries. Because of the critical nature of the parts they design and manufacture, the emphasis is always on Life-Saving Precision.