Shrink Fit Tool Holders
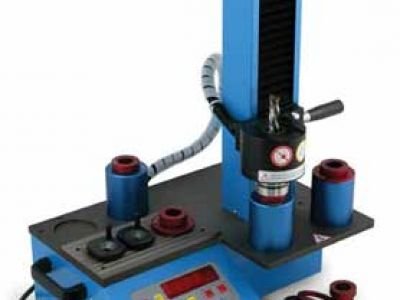
This month, we are relieved to report that most indicators, including our internal ones, say the economic outlook is improving. We are busy at Protomatic Inc., keeping pace with our customers by adding capacity to meet their growing demands. One of the ways we are improving throughput and quality is by using Shrink Fit Tool Holders. This month we are highlighting the benefits of this tool holding technique.
CAT-40 Tool Holder
This is a CAT-40 Shrink Fit Tool Holder with coolant delivery on the sides of the tool and through-the-tool coolant. Protomatic machining centers provide filtered high pressure coolant directly to the cutting edge. This improves tool life and product quality.
CAT-40 Shrink Fit Machine
This machine inductively heats the tool holder mounting end which expands the tool mounting hole. A room temperature endmill or drill is placed in the hot tool holder and the assembly is allowed to cool. As the holder cools around the tool, 10,000 lbs of clamping force is exerted. With this two improvements are realized; the tool is held tighter and more concentric to the spindle. At high RPM, the concentricity improves balance which, in turn, reducestool runout and vibration
Increasing Tool Life
The main two reasons for using a shrink fit tool holder is to increase tool life and to improve circular rotation of a tool. Typical industry observations have been that there is a 10% loss of tool life for every 0.0001” of T.I.R (Total Indicator Runout) in a machining application. In some applications, shrink fit tool holders deliver 4 to 7 times the tool life of other tool holding technologies. Shrink fit tool holders also center the rotating tool more accurately which balances the cutting forces on the tool. This translates into lower machining vibrations with better tool centerline positions often measured in microns.
Shrink Fit Holders Advantages
Improvements in tool life, cutting ability and surface finish mean less wear and tear on the tool holder (Taper Fretting), and machine spindle bearings. This is due to the tool holder’s greater clamping power compared to other tool holding methods and superior overall rigidity. Additionally, these holders have a maximum T.I.R. of 0.0001” (25.4uM), and are balanced to 25,000 RPM.
What this means to our customers
With shrink fit tool holders in place, we have a higher confidence in our “lights out” machining processes which translates into predictable tool life, production levels and shorter delivery schedules. We can also produce parts with greater positional machined accuracy.
As with all technology, sometimes one improvement opens other advantagous doors. For example, we’re now able to use equipment from Cool Blast ™ from Techniks. This equipment improves coolant application for better tool life, surface finish and product quality.
Another new, but subtle advantage is the ability to use Dual Drive ™ also from Techniks. This tooling eliminates the gap between the spindle and taper, an area that has always been a source of machining error. Eliminating this gap provides extended rigidity and accuracy. www.techniksusa.com
We’re also incorporating HeliTang ™ from Iscar for roughing. www.iscar.com
In subtle ways like this, our Machinists and Engineers are always focusing on ways to improve our quality and delivery for you.